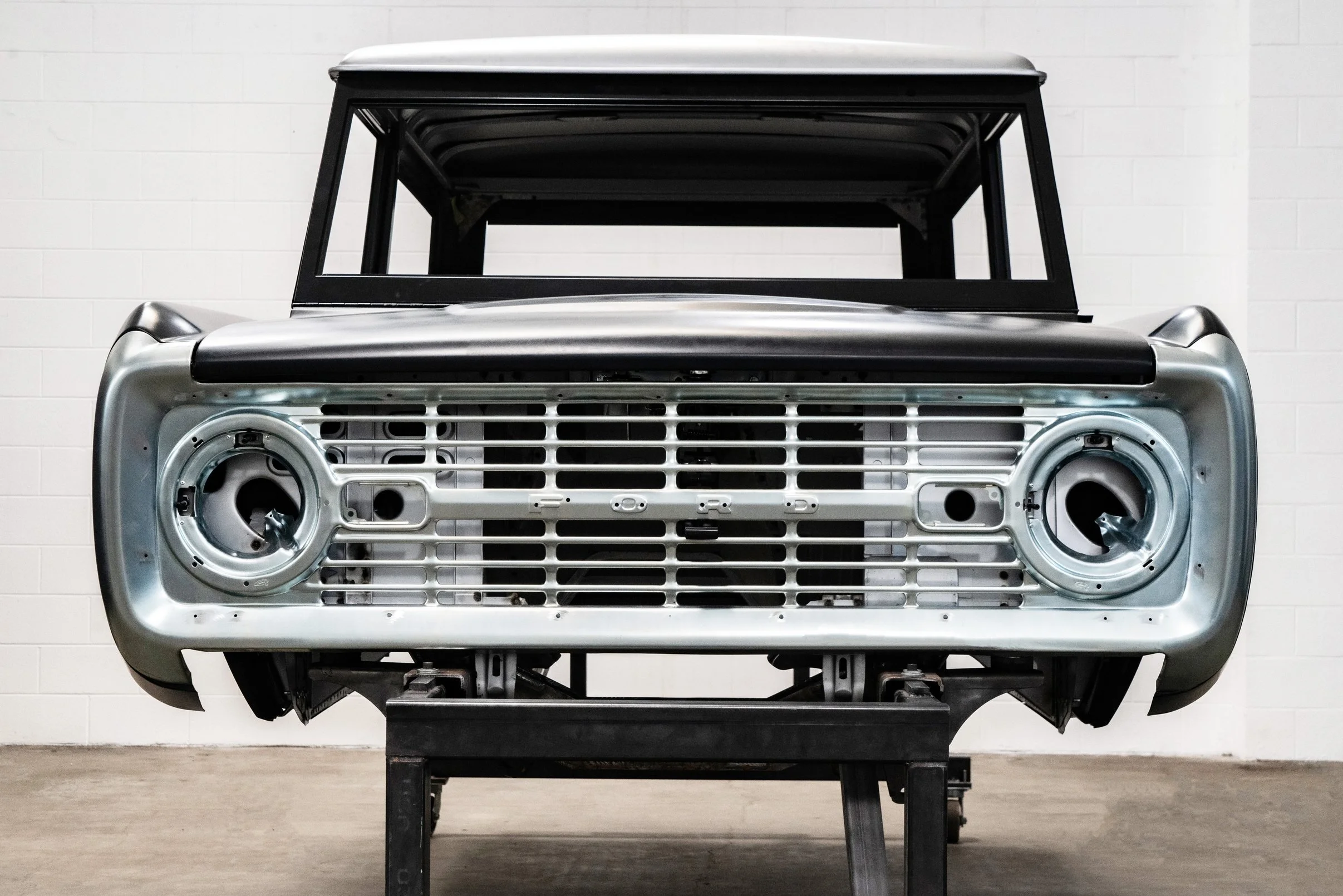
Better than factory.
The highest quality builds demand the highest quality components. To that end, Agaso Outdoor is manufacturing early Ford Bronco body tubs available to the public for the first time. Years of development have resulted in a body tub and sheet metal package that needs only to be set up on its intended frame before surfacing and top coating.
EARLY FORD BRONCO BODY
What makes an Agaso body tub different?
The idea of purchasing a body sheet metal package brand new is to take delivery of a product that solves the issues of reconditioning an original body tub. With panel stampings in a constant state of evolution, every assembly program has to evolve with them.
Until making the commitment to new bodies, the team at Agaso would spend hundreds of hours reconstructing body tubs—fixing damage from rust, collisions, and poorly executed modifications.
For quality, cost and lead time purposes, Agaso developed an in-house program that has the capacity to manufacture body tubs at scale. Body tubs that meet quality standards right off the line and eliminate the need for additional metal work. This required the dedication of resources to engineer fixtures and acquire modern, automated spot welding rigs that could execute multiple operation types as well as handle repetitive production cycles.
IMPROVEMENTS
WINDSHIELD REINFORCEMENT
Proprietary custom windshield mounts made of plate steel replace the original mounts to eliminate windshield flex.
-
From the factory, the Bronco was never intended to be driven with window frames unless it had a hard top to secure the windshield. When the top is removed the windshield frame will flex rearward at highway speeds, contact the door window frames and chip the paint on both sides. To solve this issue Agaso has redesigned the windshield mount behind the dash. This new custom plate steel mount fully replaces the original, and strengthens the base of the windshield virtually eliminating flex and the need to run bars connecting the windshield to a roll bar. It also makes it possible to hold a bikini or soft top with the windshield firmly in place. This modification is undetectable with the Bronco assembled and dash in place, and comes standard with every base Agaso Bronco body tub.
SPOT WELD PREP
All welds are properly coated with urethane compatible primer. Spot welds will rust in-transit if not protected.
-
Uncoated spot welds will rust in-transit if not protected immediately. All Agaso body welds are properly coated with urethane compatible primer so it is truly ready to surface. Cheaper lacquer-based primer coatings will react with modern auto body finishes and would result in paint defects after final coating.
TRANSPORT DOLLY
A custom dolly is included for ease of transport and proper support for the body tub.
-
This dolly is built to last and can easily be used in the surfacing, paint and liner processes.
EVERYTHING YOU WANT, NOTHING YOU DON’T
Fewer holes, fewer opportunities for unwanted fumes and heat to get into the cabin. Many factory holes go unused with modern wiring harnesses and other components.
-
Some of today’s sheet metal stampings require extensive hand work before installation, even with original tooling. Over time the tooling wears out, and quality can vary wildly compared to true OEM stampings. Metal stamping is as much an art as it is a science. Each production run of panels has its own characteristics and needs specific corrections. The mission at Agaso is to correct the imperfections so that panels can install the way they are intended, and gaps are within specification. This is a balancing act that requires skill and patience.
AFTERMARKET SHEET METAL CORRECTIONS
Today’s sheet metal stampings are not perfect, even with licensed, original tooling. Over time the tooling wears out, and quality can vary wildly compared to true OEM stampings.
-
Drilling holes after the body is painted creates issues as well, exposing the steel which eventually results in lifting paint and rust. Most Bronco builds require modifications to the factory body like filling all the holes in the firewall and re-punching the openings required for plumbing and modern wiring. This was a time consuming process when performed in the engine bay or on the underside of an assembled tub. The Agaso program allows incorporation of modifications into panel prep before assembly and welding, making these tasks more efficient and cost effective. Punching or filling holes on the bench before assembly is an easier and more efficient way to get a world-class result. This method is used on all commissioned Agaso builds, and now some of these options are available to the public. For example, Vintage Air AC kits do not use the factory heater core holes and they should be deleted, and the original wiring harness holes should be plugged as most aftermarket harnesses don’t use them. These modifications, and dozens of others, can be made for you as well as other metal prep tasks to save you time and expense, and avoid accidental extraneous holes in your custom build after paint is completed.
CONSISTENT GAPPING
The early Bronco is reliant on its frame for rigidity and therefore is a challenge to gap accurately. In addition, factory panel fitment was consistent with trucks of the day and never intended to meet modern standards.
-
Even panel gap and fitment is essential for any custom build, so Agaso created precision fixtures that rely on trusted accuracy points to ensure that not only are the door gaps even, but bolt-in parts like the pedal box will fit correctly. The end result is a product indistinguishable from an original body after it is assembled. Agaso body tubs are historically accurate and all upgrades are intended to enhance performance without sacrificing authenticity. The base Bronco body includes a standard level of gapping. Any new Bronco body tub requires final finishing if it is intended to be more than a driver. An experienced restoration body shop must spend considerable hours massaging the metal before they can begin surfacing. Specializing in this work allows Agaso to help clients mitigate additional costs with their body shop by having the body well gapped upon delivery.